MicroNet控制系统
MicroNet控制系统是目前数字式可编程控制器中的高端产品,可适用于多种控制应用:
应用
● 燃气轮机
● 蒸汽轮机
● 水轮机
● 柴油机
● 气体发动机
MicroNet控制系统能提供灵活的控制平 台,来控制各种原动机及其相关的过程, 如高速控制功能、顺序控制、辅助系统控 制、喘振控制、监控报警和测站控制等。 数字式MicroNet控制器可配置为单点或三 冗余(TMR)结构。如有需要,这两种结 构均可进行多机箱扩展,并均可支持多类 型的I/O点,包括网络离散I/O。
编程:
MicroNet控制器为编程提供了IEC1131-3 环境。
● 功能块图—采用Woodward GAPTM图 形化应用编程平台
● 顺序功能图— 用Woodward GAP语言
MICRONET TMR描述:
MicroNet TMR® 控制系统最主要的特点为采用三冗余 (TMR)结构。MicroNet TMR采用Motorola CPU (Pentium/NT CPU不支持TMR)进行双向数据交换表决和程序同步功能。MicroNet TMR包括三个隔离的单元部分, 每个部分包含自己的CPU, CPU电源和4个I/O模板。I/O模板可以为单点、双冗余、三冗余或其组合方式。每个单元的I/O部分可扩展到一个或多个MicroNet机箱, 接口模板使它们内部相互通讯。每个单元均可独立监视所有的输入数据, 执行所有的应用计算, 产生所有的输出值和响应。输出采用3选2逻辑。采用这种结构, 某一单元发生的故障将被允许。
三重化结构相对于双冗余结构的优点:
● 3选2结构对于所有的I/O、硬件和控制算法,提供了更好的错误检测
● 消除了单点故障问题 •可靠性提升至将近100% •更加灵活地实现多种容错配置 •更好的潜在故障检测
● 更高的在线使用可靠性
高密度MicroNet板卡为监控系统事件提供了首出指示, 以缩短故障排除时间。这些板卡对于开关量的采样时间为1ms, 对于模拟量的采样时间为5ms。
MicroNet TMR采用双电源,分别来自不同的源头。每个电源模板均含有三个独立的转换器, 这三个转换器分别对应一组CPU和I/O。三冗余电源结构为硬件故障提供了最大限度的保护。
Woodward为关键的开关量输出提供完全的三冗余 (TMR)继电器模块。6个继电器组合完成这种功能, 当常开配置时某一个继电器故障, 或当常闭配置时某两个继电器故障, 其接通路径不受影响, 故障将不会影响正常操作。潜在错误检测用于监测继电器故障。
MicroNet TMR控制器支持单个、两个或三个线圈的执行器。
MicroNet TMR® 实物图
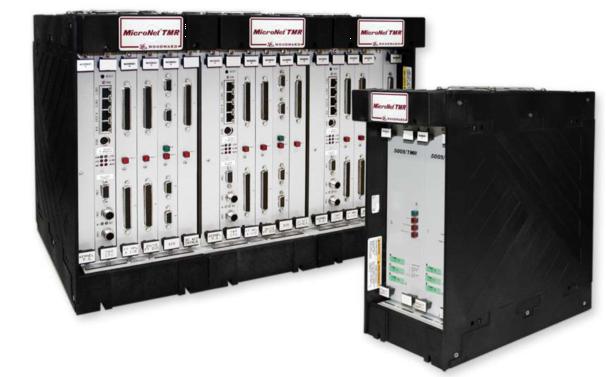
PHD实时历史数据库是霍尼韦尔公司推出的生产信息集成平台,为流程工业提供了一个用于生产实时过程管理的统一的实时数据库平台。 作为信息化的基础结构,它可以实施生产执行系统,与ERP的集成,先进和优化控制及设备管理等应用。
PHD实时历史数据库是霍尼韦尔公司推出的生产信息集成平台,为流程工业提供了一个用于生产实时过程管理的统一的实时数据库平台。 作为信息化的基础结构,它可以实施生产执行系统,与ERP的集成,先进和优化控制及设备管理等应用。
PHD不仅仅是一个实时历史数据解决方案,还是可与各流程行业用户共同成长的实时/历史业务信息平台!
特点:
● 分布式的冗余数据采集方案,确保数据的不间断归档
● 毫秒及数据精度,优化的历史数据存储策略极大的扩展了数据存储量
● 可靠的多线程数据库内核设计,确保对重要生产过程数据的可靠管理
● 独特的数据库自动诊断功能,及独立于数据采集时间的数据自恢复
● 专用的产品化实时数据库接口RDI,使其像DCS一样长期稳定运行
● Workcenter最新的实时数据网络展示发布技术,采用.NET网页服务和B/S解决方案。
数据库整体结构:
PHD一体化数据库平台包含实时数据库、事件数据库、事务性数据库和应用数据库,可以存放不同类型的数据,支持不同的上层高级应用。
● 实时数据库用于保存和管理过程的实时数据,如测量值等。
● 事件数据库用于保存过程报操作信过程变化信息和SOE事件等
● 事务性数据库用于保存实验室分析结果,物料移动数据,设备产品信息等
● 应用数据库用于支持一些特殊应用,如物料平衡、操作管理、绩效管理和先进控制等
PHD数据库整体结构图:
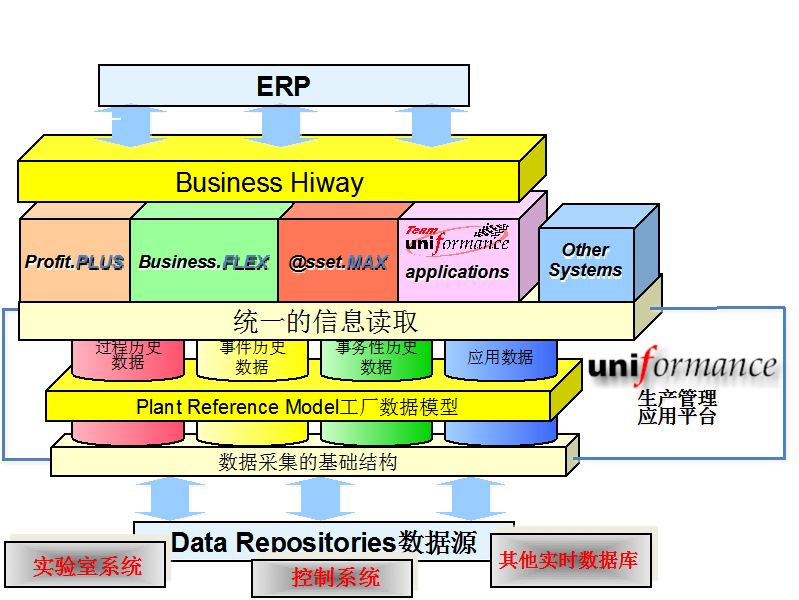
PHD作为SIS系统数据平台系统图:
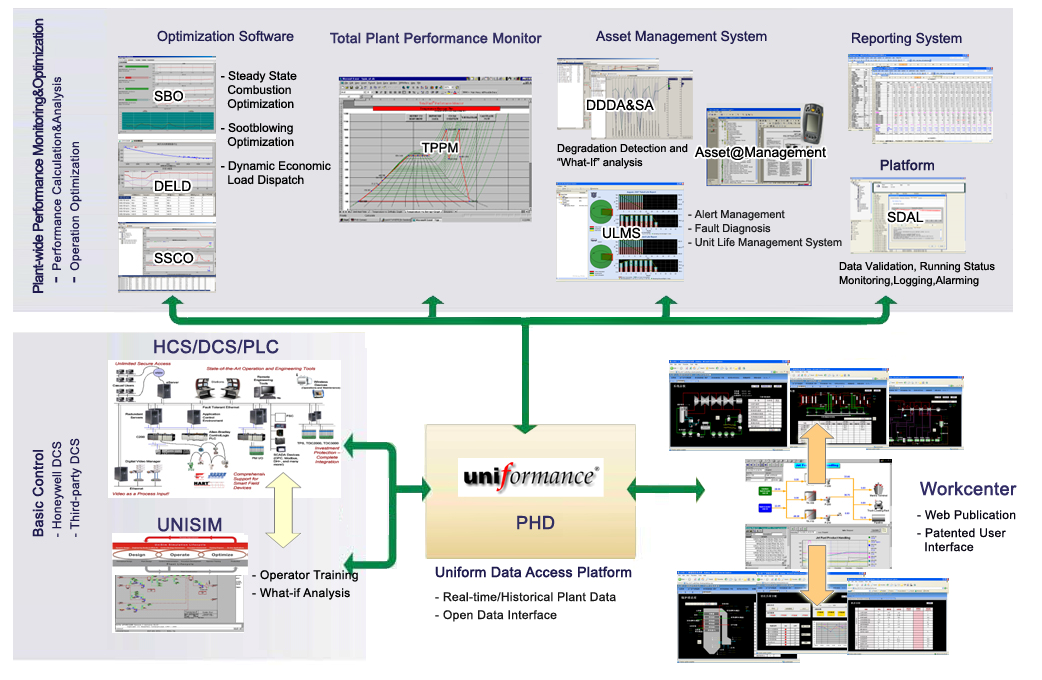
PHD 组件和数据流图:
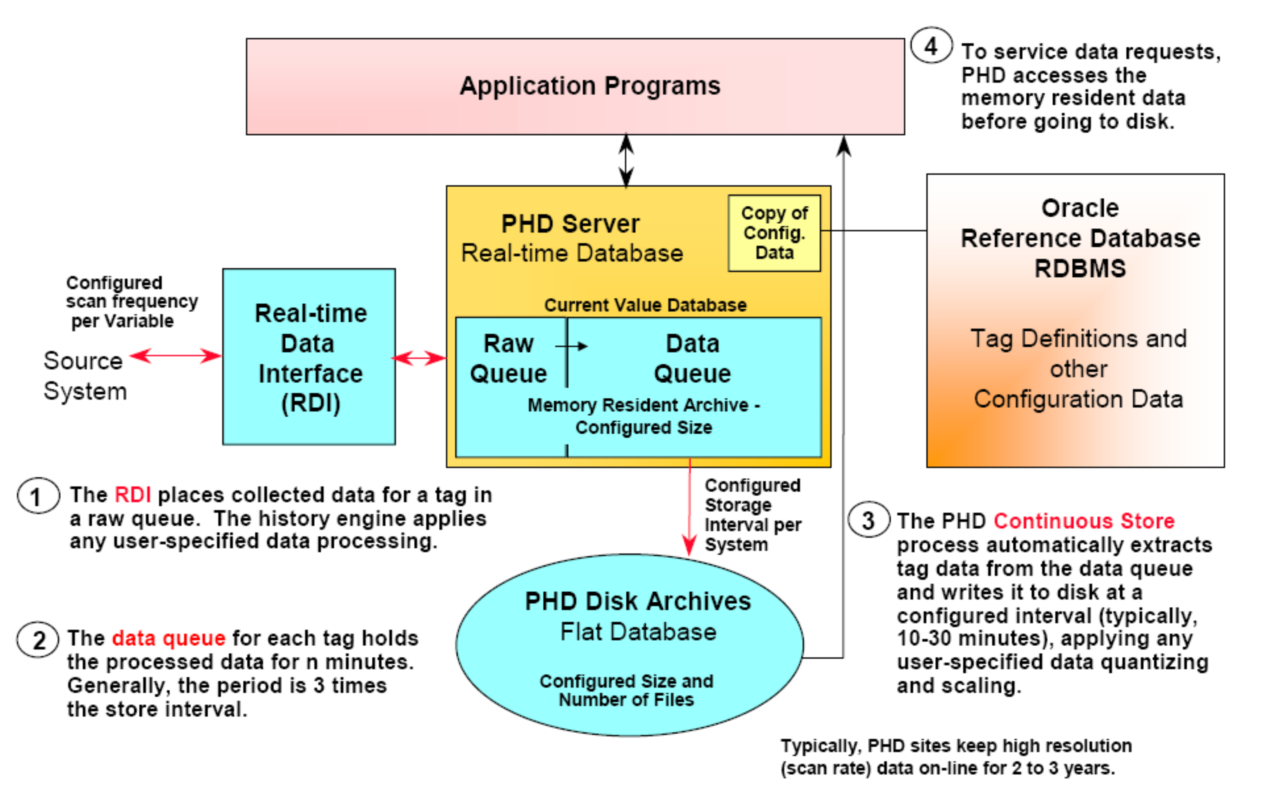
锅炉优化控制系统
概述:随着机组容量、运行参数的提高、负荷需求, 迫使参与调频的机组负荷频繁波动, 导致运行过程中过程变量产生较大的偏差, 需要运行人员手动干预才能保证生产过程的正常运行, 原有的PID控制系统已难以满足电力生产的要求。 同时由于近年燃料价格的逐节攀升, 以及电力行业减排的繁重任务, 寻求电力机组的节能减排措施已成为电力生产企业所面临的问题。
先进优化控制技术具有优化、自适应、自学习等功能,在现代电厂的控制与优化运行中逐渐显露优势。
锅炉优化控制系统是在机组原有的 DCS上层增设装有先进控制器软件的上位机, 通过 Modbus/OPC 接口与 DCS 系统连接。 先进控制器从DCS中采集相关的运行数据, 计算出当前时刻的控制指令最优值, 通过 Modbus/OPC 接口发送到 DCS 系统, 由 DCS 送到现场执行装置执行。
锅炉优化控制系统采用多变量模型预测控制(简称 MPC) 算法。 MPC 是一种基于模型、滚动优化并结合反馈校正的优化控制算法。 模型预测控制综合利用实时信息和模型信息, 对目标函数不断进行滚动优化, 并根据实际测得的对象输出修正或补偿预测模型, 具有自适应功能。它可以有效地抑制各种扰动因素对被控变量的影响, 使机组在受到频繁和大幅度扰动的情况下仍能保持良好的控制品质。同时它还考虑机组运行中包括设备安全在内的各种约束条件, 能在严格满足约束的情况下使设备运行在最佳工作点附近, 实现“卡 边”控制。
一、先进优化控制技术在电力机组主、再热蒸汽温度控制中的应用
1、主蒸汽温度先进控制系统标
基于多变量模型预测控制技术的主蒸 汽温度先进控制可以改善蒸汽温度控制系 统的动态特性,提高锅炉出口过热蒸汽温度 的稳定性,减小过热蒸汽的温度变化范围, 进而允许过热器在更高温度上运行, 获得更高的热效率。
主蒸汽温度先进控制系统在 300MW 机组上的投运效果如下表所示:
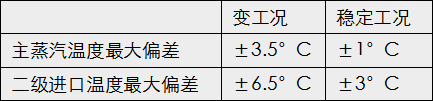
2、再热蒸汽温度先进控制系统
基于多变量模型预测控制技术的再热汽温先进控制可以有效地克服主汽温系统和再热汽温系统相互之间的耦合。系统投运后,可在变负荷工况下将再热蒸汽温度控制 在±4°C之内。
二、先进优化控制技术在电力机组燃烧控制系统中的应用
我国燃煤机组锅炉燃用的煤普遍存在着煤种多变, 偏离设计、煤质劣化、着火困难和燃烬差等问题, 因此煤质的变化成为机组运行过程中一个重要干扰因素。煤质的在线监测和识别已成为燃烧先进控制系统中非常必要的一个技术内容和手段。
燃烧先进控制系统的结构主要包括煤质实时在线检测和燃烧控制优化系统两部分。
煤质在线检测装置采用火焰闪烁特性、光谱特性、燃烧后烟气组分、炉膛温度特性等多源数据融合的手段, 实现机组当前燃用煤质的在线检测和辨识。燃烧控制优化系统包括静态和动态两层优化。静态优化是利用建模技术结合当前 行数据, 给出在机组当前运行工况下最佳燃烧静态参数,作为设定值提供了实时优化的目标。动态优化是采用多变量模型预测控制算法, 根据机组当前工况在多目标多约束条件下实时在线寻优, 实现在保证机组锅炉安全运行和污染物气体排放达标的前提下, 锅炉的效率接近最优。
燃烧先进控制系统投运后可达到的技术指标如下表所示。
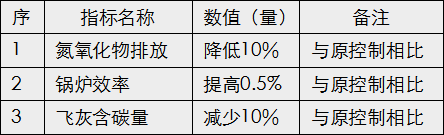
三、先进控制系统投运后的经济效益分析
在电力机组上应用先进控制技术实现机组的优化运行, 不仅可以有效地提高机组运行的安全性,还能很好地提高机组运行效率, 减小机组氮氧化物的排放量,对实现电 力机组的节能减排目标有重要意义。
以 300MW 机组为例,主、再热蒸汽温度先进优化控制系统投运后的直接经济效益为人民币 500 万元/年左右(按汽温平均运行值 提高 3°C计算), 锅炉燃烧先进控制系统投运后的直接经济效益一般为人民币 300~600 万元/年以上。
冷机站是中央空调的冷热源,它消耗建筑物日常能耗的30%-50%。通过我们的优化控制系统,能帮助冷机站在常规控制基础上节约15%-30%的能耗。它采用了自适应的仿真技术在计算机上建立虚拟的冷机站模拟当前空调方案的运行,并在作出控制决策前,使用优化模型来预测控制结果,选择最优的控制方案输出到冷机系统。这个最佳方案能够利用冷机站的各项潜力,在一段时间内协同各部分以最高的方案效率提供所需制冷/热量。
优化控制系统特点:
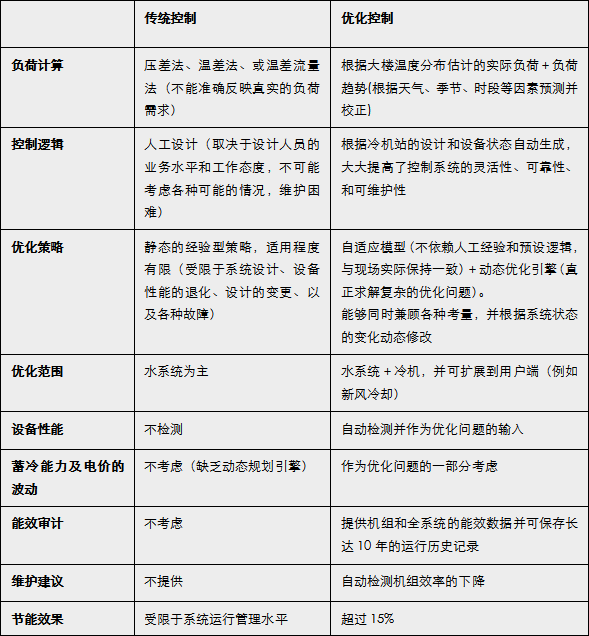
空分优化控制系统
概述:采用基于模型预测(MPC)的优化控制技术实现空分装置的优化目标。
空分装置的优化控制目标主要有:
● 空分装置的变负荷控制,即根据氧的需求量,并据此控制装置的负荷变化
● 实现各产品质量的卡边控制,提高最有价值产品的收率(氧、氮、氩)
● 降低空分装置的总体能耗,包括提高压缩膨胀机和冷箱系统的能量使用率等
并兼顾其它基本控制要求::
● 实现空分装置的安全平稳操作
● 保护装置各工艺设备的约束
● 在氧的需求发生改变时,快速准确地平稳装置的操作
● 控制各产品(氧、氮、氩)的纯度
空分装置的优化控制系统的效益有:
● 自动变负荷 – 能降低约25%氧气放散量
● 提高产品收率 – 能降低产品质量的标准偏差50%左右
● 降低总体能耗2%左右
● 延长设备使用寿命
优化控制原理图:缩小偏差,提高收率
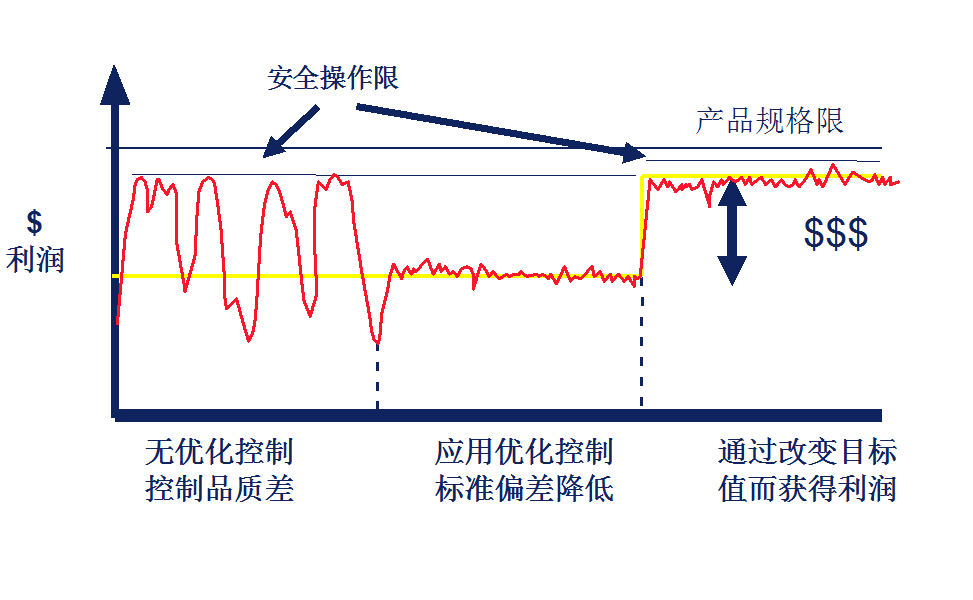